Process flow
In the field of glass pretreatment equipment, our company uses exquisite craftsmanship and rigorous processes to create high-quality equipment for customers.
1. Design and Planning
Our team of professional engineers will first communicate with customers in depth to understand their specific needs and production goals. Based on this information and combined with new technology trends in the industry, we will carefully design a more optimized equipment solution. From the overall architecture of the equipment to every detail component, it has been repeatedly demonstrated and simulated to ensure the scientificity and feasibility of the design.
2. Raw Material Procurement
We adhere to strict standards for the selection of raw materials. We only work with reputable and reliable suppliers to ensure that the purchased raw materials such as steel, electronic components, transmission components meet high quality requirements. Each batch of raw materials must undergo strict quality inspection before entering the warehouse, and only qualified materials can enter the production line.
3. Parts Processing
In the modern processing workshop, high-precision machine tools and advanced processing technology process raw materials into various precision parts. Skilled workers strictly follow the design drawings to ensure the dimensional accuracy and surface quality of each component. After multiple processes of processing and inspection, unqualified parts will be eliminated in time to ensure the overall quality of the equipment.
4. Assembly and Debugging
Carefully assembling the processed parts is a process that requires high patience and care. The tightening of each screw and the connection of each wire are crucial. After the assembly is completed, strict debugging work is carried out. By simulating the actual production environment, the various performance indicators of the equipment are tested and adjusted to ensure the stable and efficient operation of the equipment.
5. Quality Inspection
Before the equipment leaves the factory, our quality inspection team will conduct a comprehensive and strict quality inspection. From appearance inspection to performance testing, no detail is missed. Only equipment that passes all inspection items will be labeled as qualified and ready to be delivered to customers.
6. After-sales service
Our service does not stop at the delivery of equipment. During the process of customers using the equipment, we provide timely and professional after-sales service. Whether it is equipment installation guidance, operation training, or troubleshooting and maintenance, we are always available to support customers to ensure that customers' production is not affected.
Our company always provides customers with reliable glass pretreatment equipment with rigorous process and excellent quality pursuit, helping customers stand out in the industry.

CNC laser cutting machine
1. According to the workpiece drawing, use CNC laser cutting machine to carry out CNC sheet cutting.
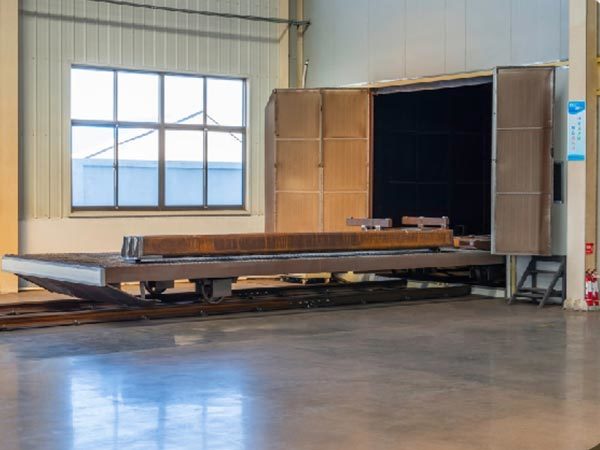
Sandblasting room
2. The sandblasting machine is equipped with environmental protection equipment DMC250A and 18,000 air volume dust collector, which can remove rust on the surface of the workpiece and enhance the surface hardness of the workpiece while ensuring environmental friendliness.
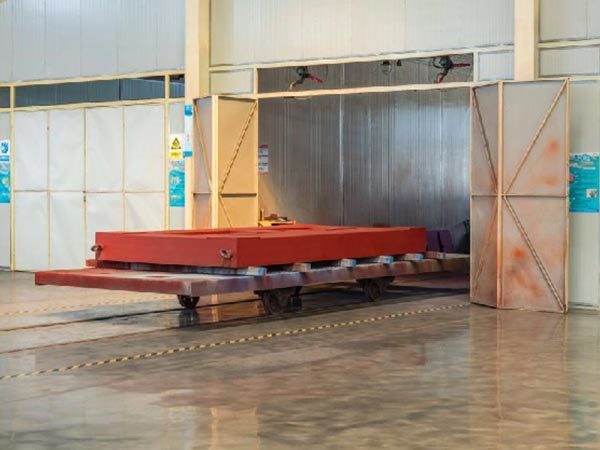
Paint spray room
3. The painting equipment is equipped with 20,000m³/h honeycomb activated carbon adsorption + desorption + catalytic combustion environmental protection equipment to protect the physical and mental health of employees and the atmospheric environment, and complete the surface coating of the production equipment to achieve the requirements of beautiful and pleasant surface of the workpiece.
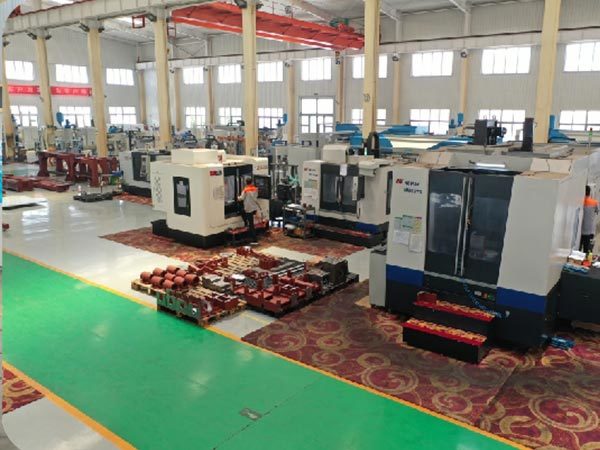
CNC machining equipment
4. The standardized processing workshop has multiple CNC processing centers: ● Horizontal processing center HM63TD (brand NEWAY) ● Vertical processing center VM1150S (brand NEWAY) ● Fixed beam gantry processing center (4 meters) GLU28X40L (brand HISION) ● Fixed beam gantry processing center (8 meters) GRUII32X80 (brand HISION)
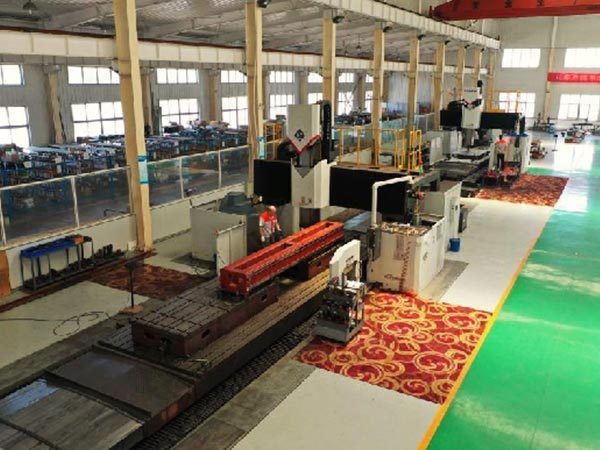
CNC machining equipment
5. After the surface of the metal workpiece is sandblasted and painted, it is transferred to the processing workshop and processed and manufactured using high-precision CNC machine tools. At present, all the main core components are self-made to ensure that each customized glass processing unit is equipped with high-quality components; at the same time, the delivery time stipulated in the contract can also be strictly guaranteed.
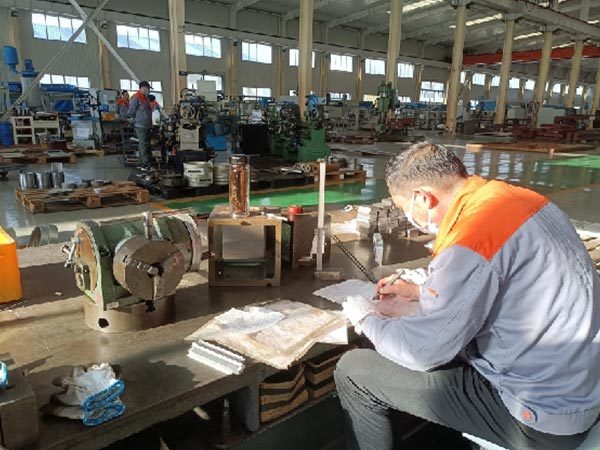
Processing parts inspection
6. After the parts are finished, professional quality inspectors will check the processing size and accuracy of the parts.
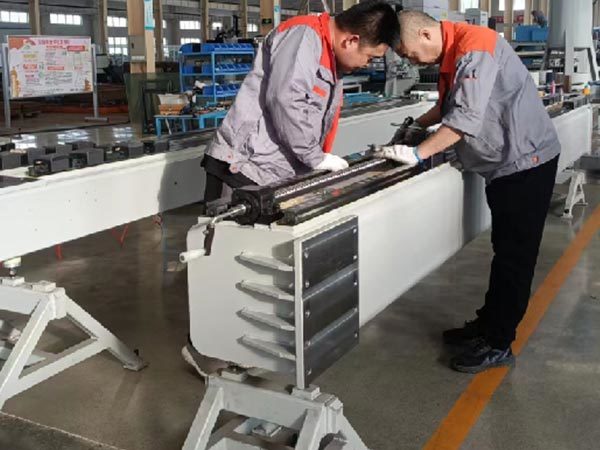
Assembly process
7. Parts that have passed inspection and completed surface treatment will be transferred to the assembly workshop for assembly.
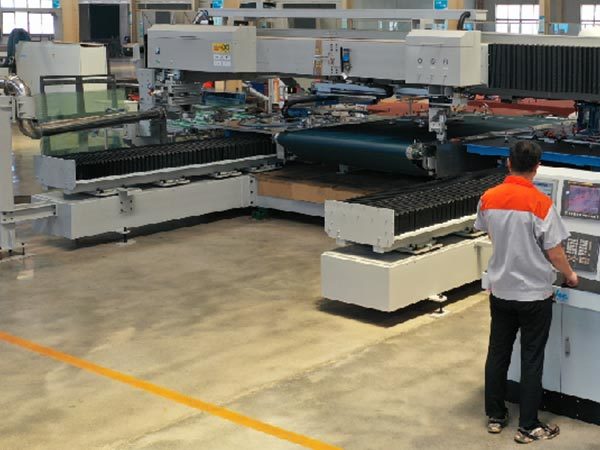
Debugging process
8. After the equipment is assembled, carry out power-on debugging and glass test cutting.